I had the pleasure to be invited by Jan Helmig and Jochen Hardt at Covestro HQ located in Chempark, Leverkusen.
Chempark is covering a 11 km2 total area, including 85km pipe bridge, 45,000 employees, 102 km factory roads, 102 km tracks and 500 enterprises. And it is obviously the historic location of Bayer
Covestro is a key player in the automotive lighting industry, as one of the main player in optical plastic raw material supply. Without any polycarbonate, we would still have glass lens, rectangular headlamp shape and most of all the latest innovation in our field would not have been possible.
Company started in 1863, founded under the name “Friedr. Bayer et comp.” in Barmen, today a district of Wuppertal. Company started to manufacture and sell synthetic dyestuffs from coal-tar. In 1937, Otto Bayer discovered Polyurethanes and in 1954 Hermann Schnell invented Polycarbonate and from this time, Covestro has built a reputation as industry pioneer.
In 1980s, Covestro delivered Makrolon© for the first Automotive headlamp lens. In 1993 the polycarbonate headlamp lens of Opel Omega was the first one in Europe.
On September 1st, 2015, Bayer MaterialScience became a separate legal entity operating under the name Covestro, with Headquarter remaining in Leverkusen.
Covestro generated sales of EUR 14.1 billion in fiscal year 2023. At the end of 2023, the company had 48 production sites worldwide and employed approximately 17,500 people (calculated as full-time equivalents).
Covestro is still on the top of the innovation with remarkable innovative products they have revealed in the last few months:
- Recycled Polycarbonate from old tires
- PU coating for front grills (BMW iX), including film integration
- PC-Heatsink as alternative to aluminum heatsink
- Diffusive EL polycarbonate for edge light design
- Imagio® OMD
At the same time, Covestro is investing in optical lab to be able to support lidar measurement (and lidar integration behind PC-lens) and has just released an optical database with all their PC optical properties to accelerate the work for tier1 and OEM for optical simulation and testing.
Recycled Polycarbonate from old tires
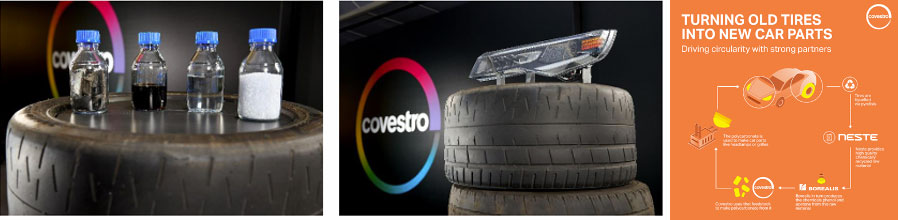
Neste, Borealis and Covestro have signed a project agreement to enable the recycling of discarded tires into high-quality plastics for automotive applications. The collaboration aims at driving circularity in plastics value chains and the automotive industry. When no longer fit for use, tires are liquefied by means of chemical recycling and then processed into base chemicals and further into polycarbonates of high purity. These can then be used in various automotive applications, from parts of headlamps to radiator grilles.
As part of the collaboration, Neste turns liquefied discarded tires into a high-quality raw material for polymers and chemicals manufacturing and supplies it to Borealis. Borealis will then process the Neste-produced raw material into base chemicals phenol and acetone, which are supplied to Covestro. Covestro can use these materials to make polycarbonates. The share of recycled content is attributed via the mass balancing approach all the way to the final products using ISCC Plus certification.
The first products based on the collaboration are already available as each party has manufactured the first batch of their respective contribution to the project. Aside from polycarbonates, the project partners may also consider polyurethanes as a possible end product, which could also find its way into parts of the interior of a car. The companies emphasize that the potential to scale-up these types of developments should be considered when setting ambitious targets for future EU regulations, such as the End of Life Vehicles Regulation.
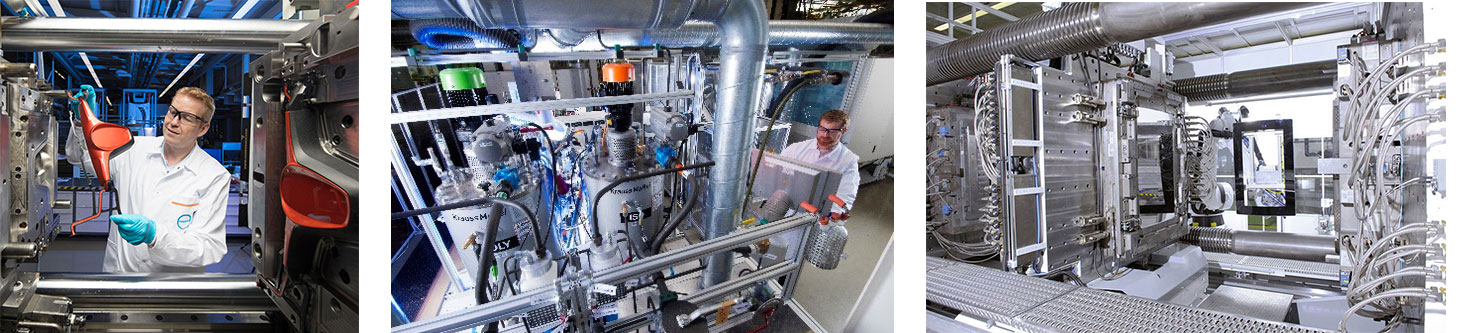
The combination of Injection Compression Molding, In-Mold-Coating and partial Film-Insert-Molding enables a novel design like the one on the BMW iX front panel (Kidney):
- Integration of medium range RADAR behind the kidney panel without any air gap
- Defrosting system with heating film integrated in the PC layer
- Multicolor class A finish
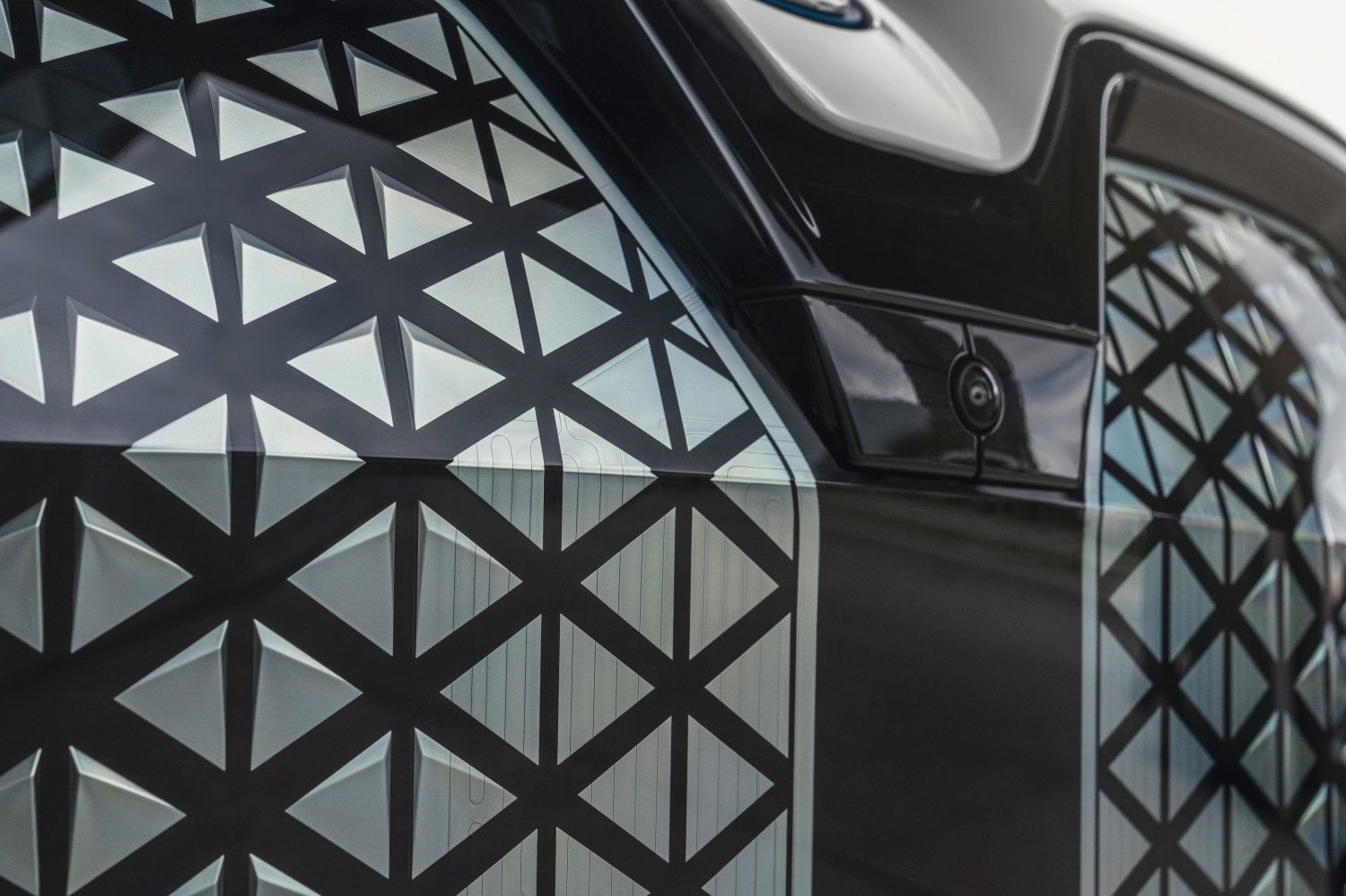
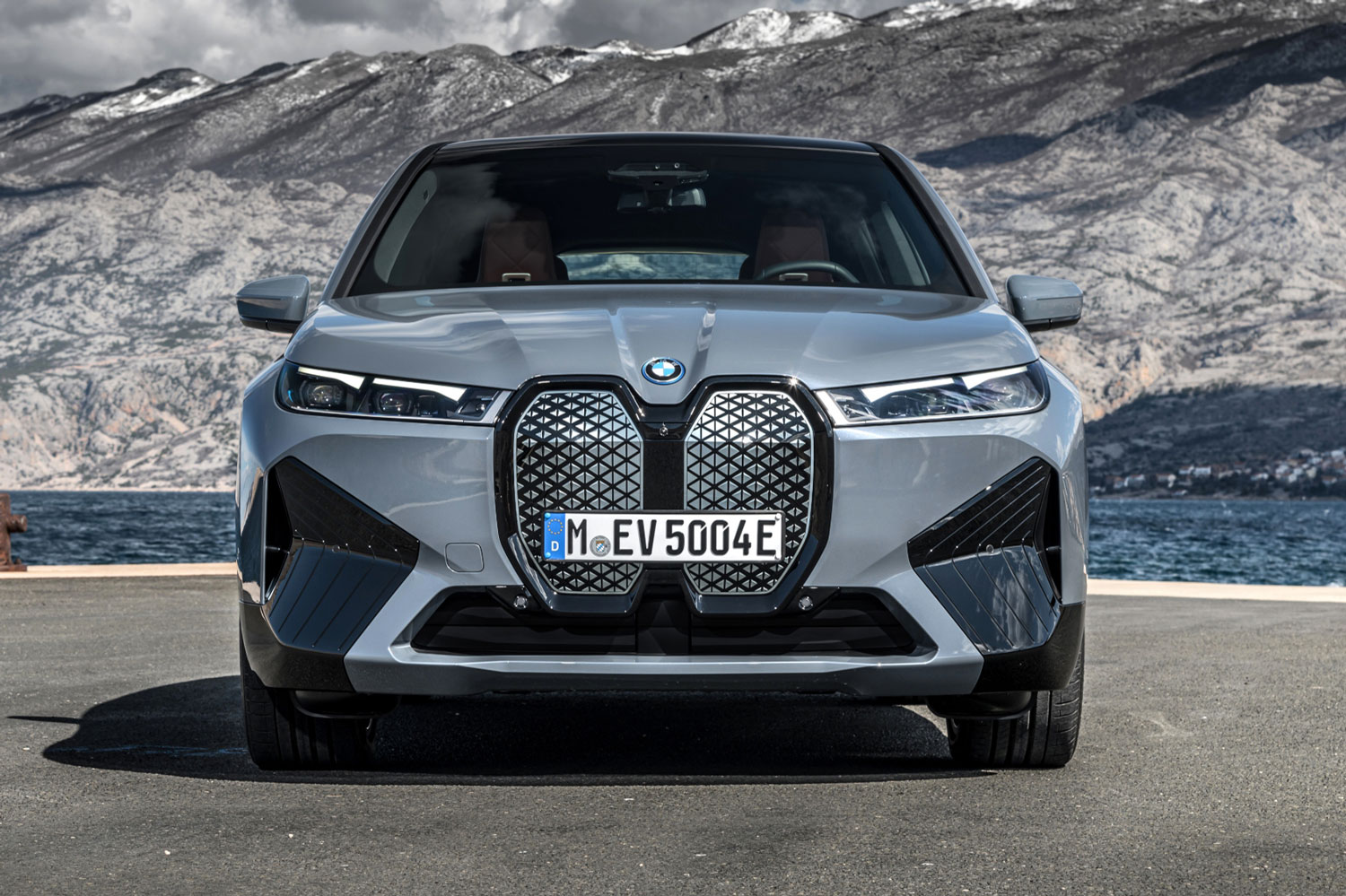
To be able to realize this design, different steps are needed to succeed:

- 3D structure with prisms of varying depth integrated in a transparent PC base substrate with compression molding process (compression process interest is to reduce and homogenize pressure during injection, thus reduce warpage, sink marks and inner stress.) Addition of a 3D PC heating foil on A-surface (Film Insert Molding)
- PUR (Polyurethane) coating layer to obtain a class A finish
- Black Painting on the B-side
- partial laser etching of black paint
- PVD (physical vapor deposition) process with metallic appearance
- Black protection on the B-surface
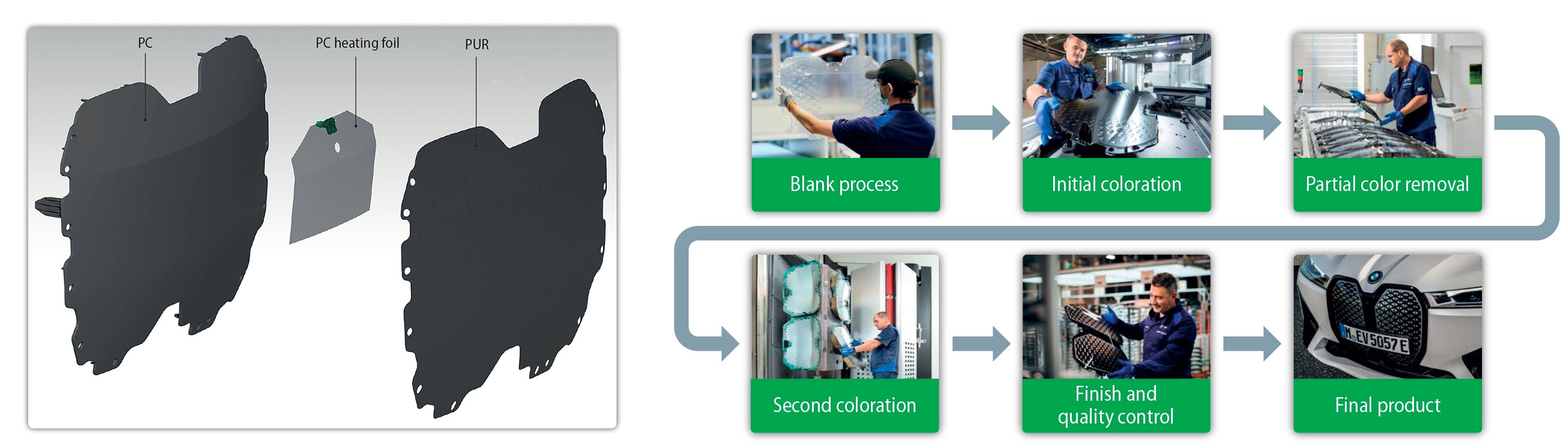
PUR Coating layer is based on Covestro´s raw materials Desmodur and Desmophen. It imparts high scratch resistance to the component finish and is self-healing. Minor scratches simply disappear on their own after a short time (see video extract from BMW : (2) Video | Facebook)
This technology is replacing classical spray coating process including multiple steps (injection, storage, cleaning, pre-treatment, coating, curing) by a 2K injection process. Other advantages are the possibilities to have sharp 3D structures or replication of delicate mold structures.
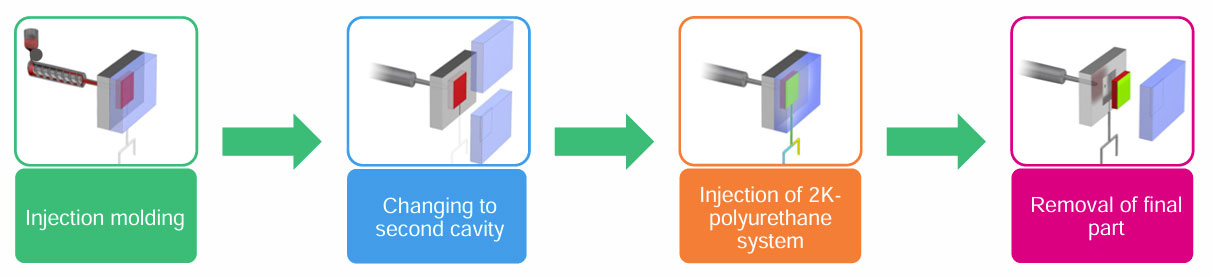
Compression molding (ICM) is used to reduce internal stress (lower pressure during injection, lower clamping force)), improve surface replication, reduce sink marks, improve optical properties and improve geometry tolerances. Injection is done in two steps as described below:
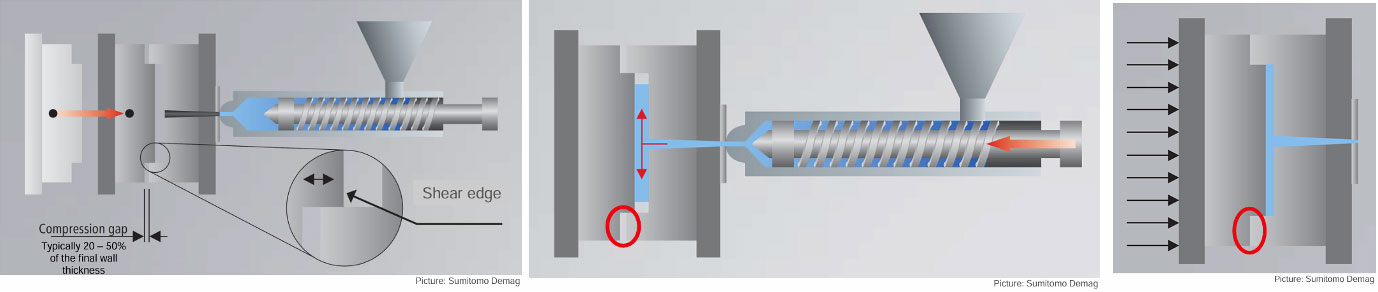
Thanks to this technology, Covestro claims filling pressure reduction potentials of 40% and more.
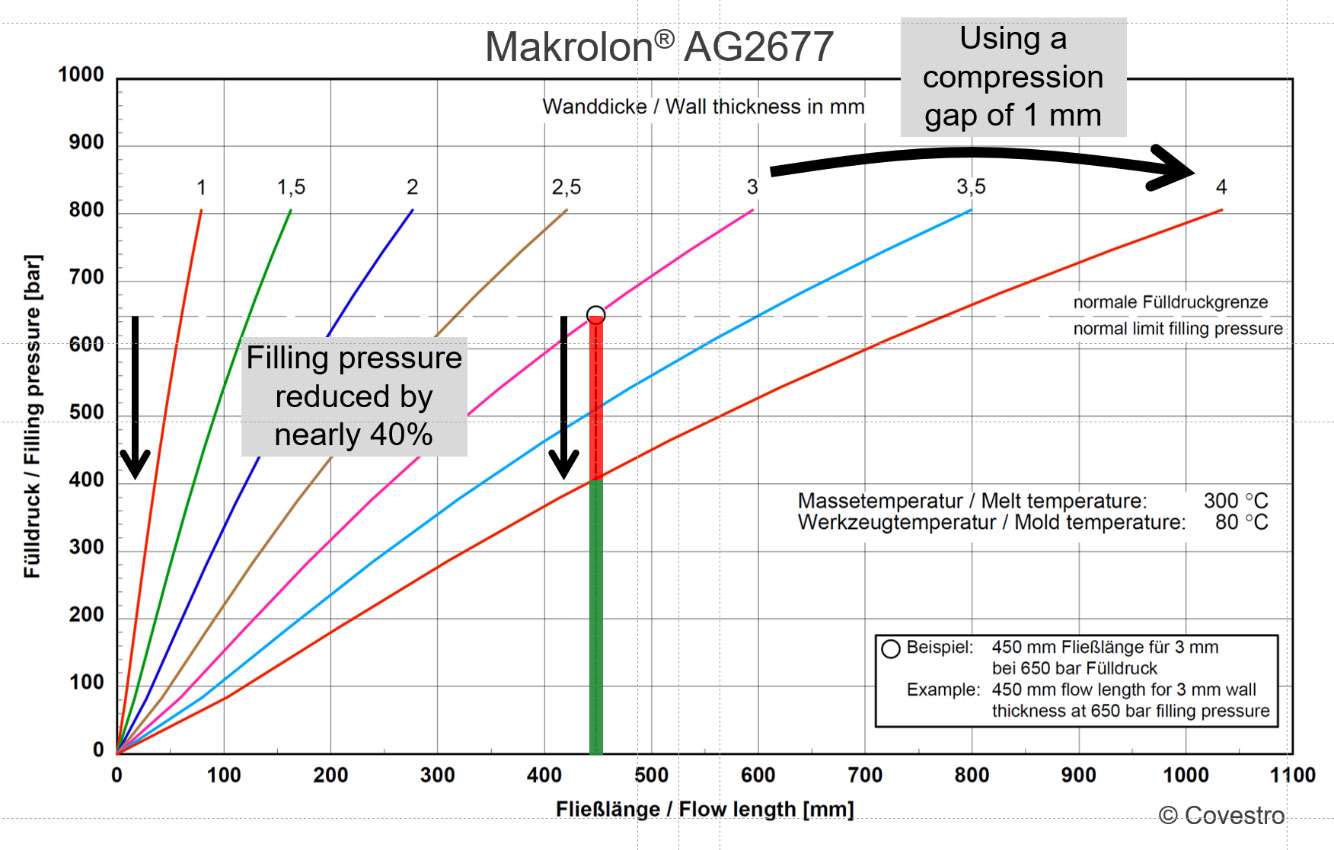
Covestro provided detailed support to BMW in the development of the front panel. Various development molds were trialed at Covestro’s technical lab in Leverkusen, in addition to Covestro extensive simulations on the rheological behavior of both injection compression molding material and the PUR reaction system during mold filling.
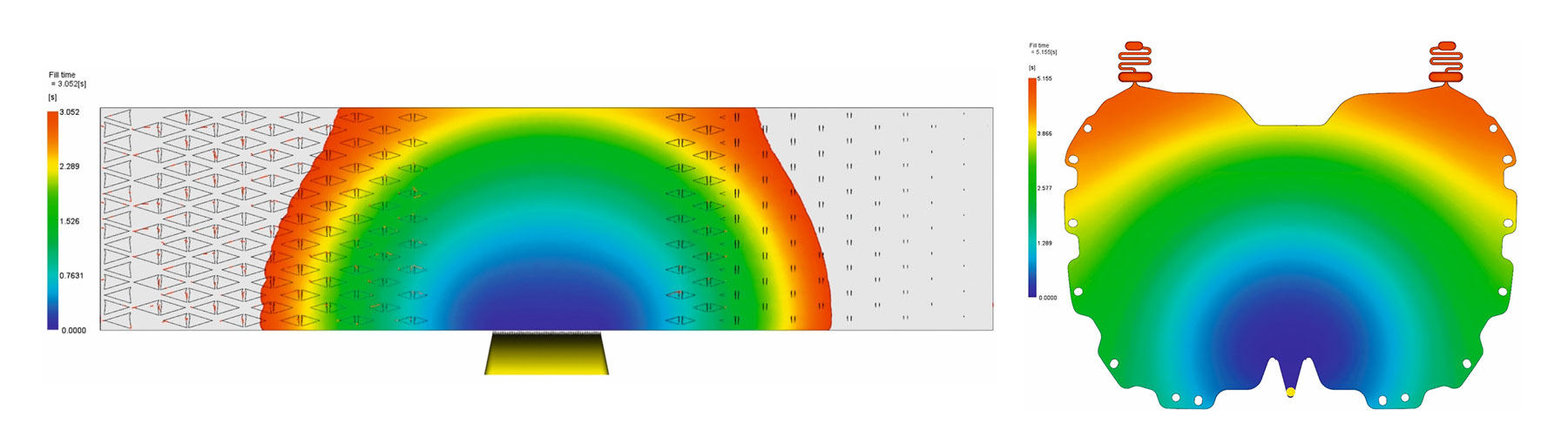
PC-Heatsink
Covestro has developed with partners an integrated solution for low beam / high beam optical system :
- No Fasteners or Thermal Interface Material (TIM) : LED chip are directly integrated in injection tool (insert molded electronics)
- No aluminum : aluminum heatsink is replaced by PC-heatsink made of Makrolon© TC
- All-in-one heatsink and reflector injection in a 2K shot
- Possibility to use recycled PC
This solution is offering similar thermal dissipation properties compared to aluminum with possible weight reduction and cost savings.
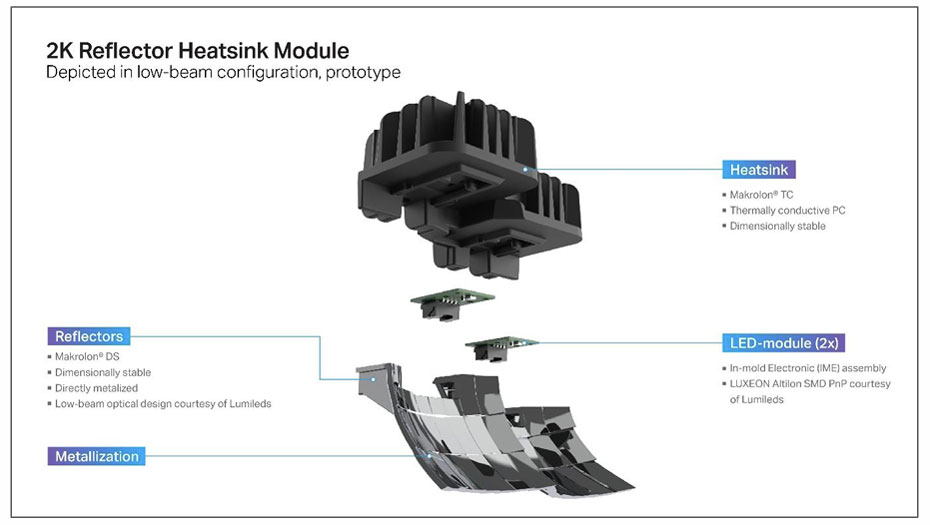
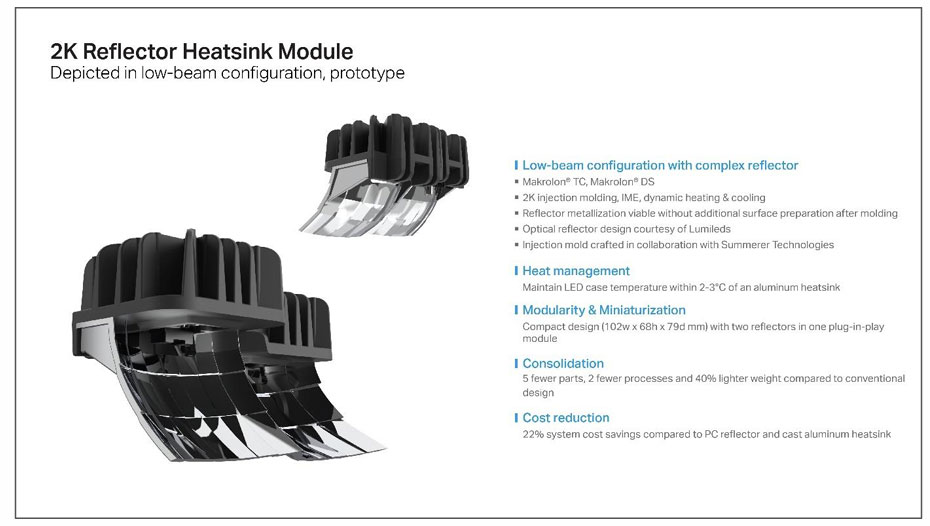
Diffusive EL Polycarbonate
Covestro has developed a transparent Polycarbonate grade that become milky / opalescent when we apply light from the edge. Different transmission values can be obtained
This concept can be implemented in a lot of design proposal for position lamp application
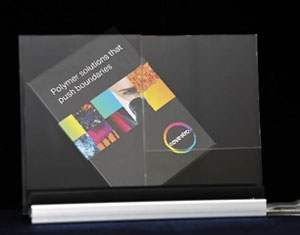
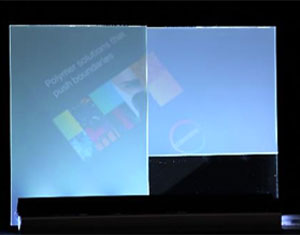
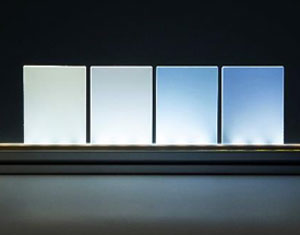
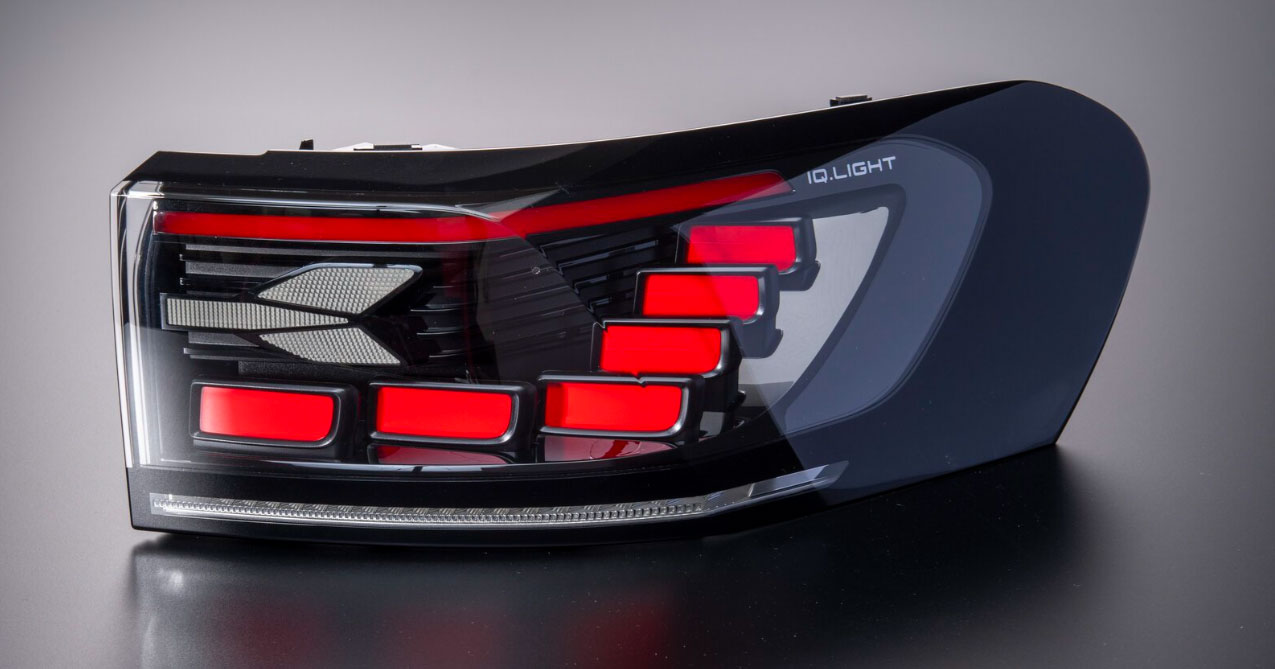
Laser welding technology for headlamp
Covestro have investigated with Branson / Emerson laser welding to replace the “state of the art” headlamp assembly (PC lens, PP housing and glue between both components).
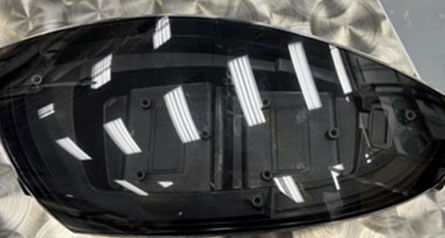
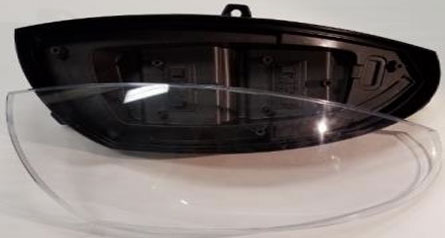
By replacing PP by PC/ABS, laser welding is feasible. Advantages can be summarized as below :
- Improved cycle time
- Enhanced recycling (no need to separate lens, housing ang glue for refurbishing)
- Better geometry of final product
- Elimination of pre-treatment on PP
- No need to hide the gluing channel by hood / bumper / fender components
- No risk of glue outgassing
- Potential dis-assembly of lens and housing using an “un-welding” process
Preliminary testing shows good impact resistance, no air leakage, and acceptable burst strength of the welded headlamp.
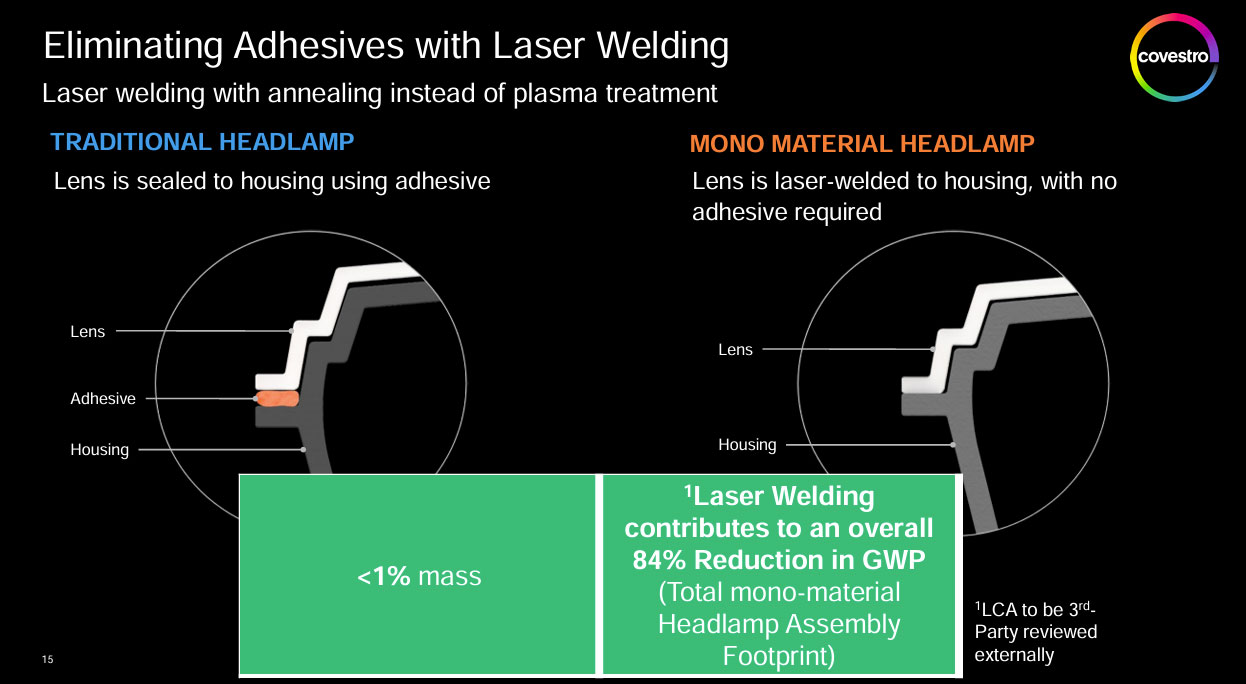
Imagio® OMD
Covestro has developed a database to accelerate optical simulation and give more speed from design to production.
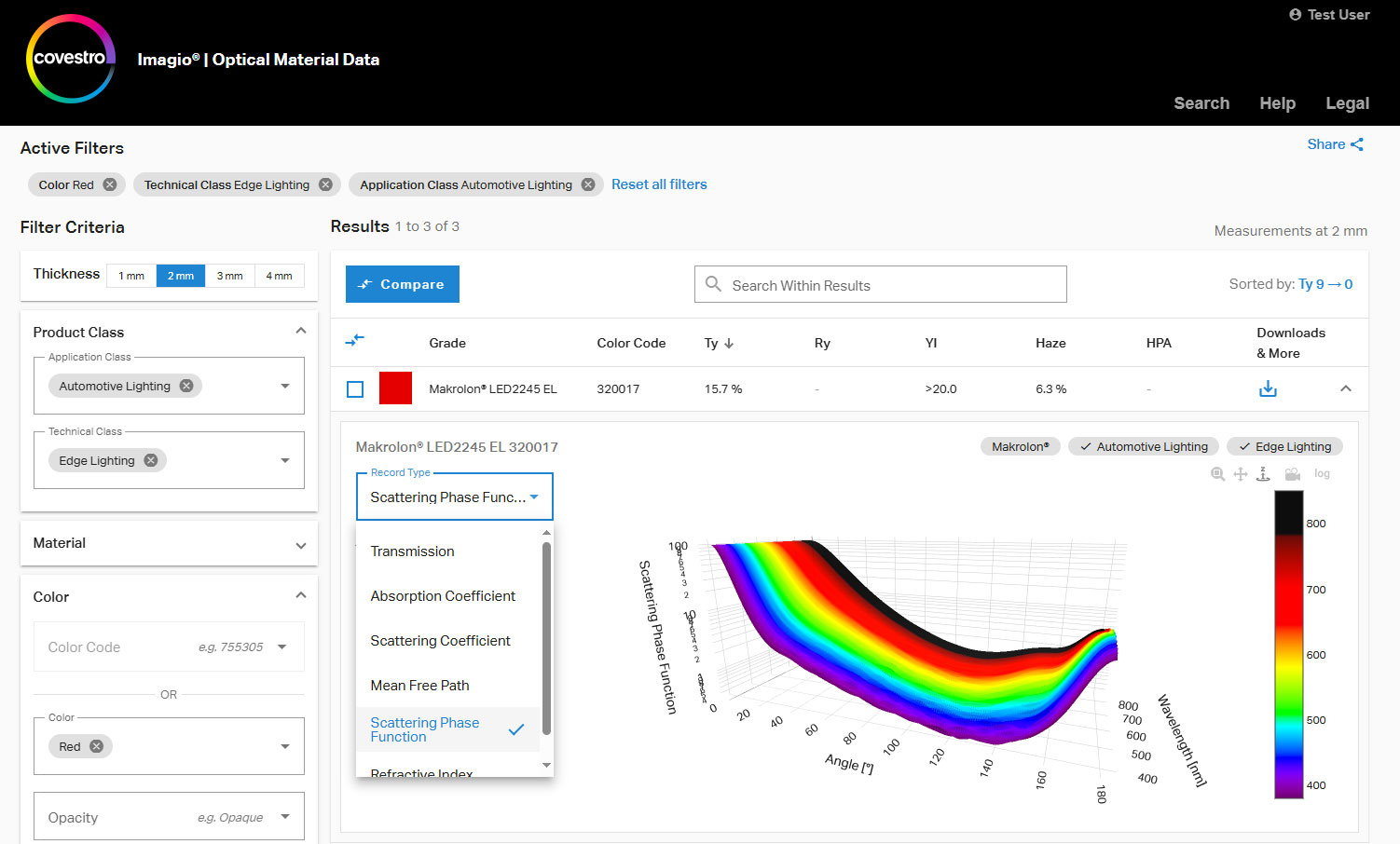
Imagio® CQ program enables customers to make a material decision more quickly and generate and visually evaluate sample parts in the early stages of development. This saves time and costs during specification, and the suitability of more sustainable plastics can also be tested at an early stage. In the three dimensional space of color, material and finish (CMF), the possibilities are almost unlimited. The backbone of the digital solution is X-Rite/Pantone’s Total Appearance Capture (TAC) technology, which captures optical properties such as color, gloss, transparency, translucency or texture of a specific material sample using an optical appearance measurement device. The data is stored in a special data format. This is supported by leading rendering software tools that Covestro customers use for their design and marketing visualization. Covestro’s Color & Design Centers (CDCs) in Filago, Italy, Newark, USA, and the Caojing and Guangzhou facilities in China are already equipped with the technology to create digital twins of materials. A new tool for sales and marketing to search for color combinations – the Imagio® Color Finder (ICF) – also serves to achieve this goal. Overall, Covestro expects a shift from costly color matching requests in the CDCs to existing color codes with a better search experience. The Imagio® CQ family has now been expanded to include a module called Imagio® Optical Material Data. The target group here are experts from the field of development and simulation of optical components, i.e. vehicle headlights and interior lighting, as well as general lighting. The module is already being tested with customers and will be the first Imagio® module to be available after the required registration. On the one hand, it will be possible to search specifically for optical material properties in our EP portfolio, and on the other, Covestro will provide the necessary data for optical simulation programs such as Ansys Speos, Optis LightTools or customers’ own simulation solutions.