Car designers have a passion for decoration because it goes beyond aesthetics to create an emotional connection between the driver and the vehicle. Decorative elements make a car feel personal, luxurious, and unique. They guide perceived quality and craftsmanship, which are pivotal in the competitive automotive environment. The interior is where drivers and passengers spend most of their time, so optimizing that space significantly drives the overall user experience.
Innovative decoration techniques like IMD, IML, and IME allow designers to incorporate functional elements seamlessly into their designs, making the car not just beautiful but also functional and technically advanced.
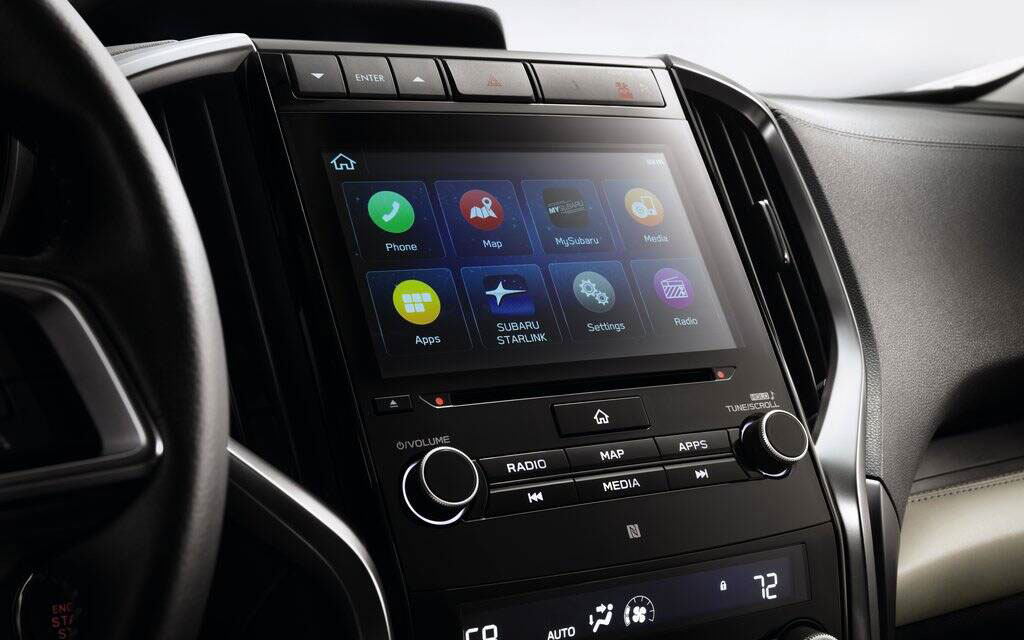
In-mold decoration (IMD)
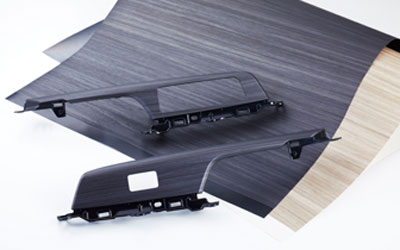
IMD is used to create visually attractive surfaces on automotive parts. It involves printing patterns on a film, which is then placed into a mold and injected with plastic in a single step operation. This process is used for dashboards and dashboard inserts; door panels and inserts; steering wheels; trim panels; seat backs, and storage compartments.
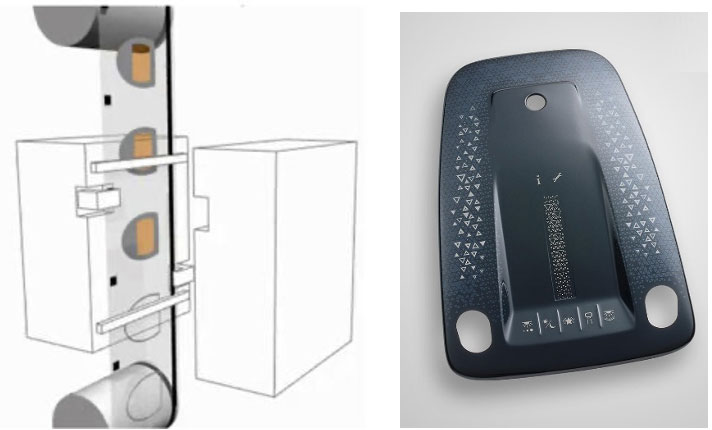
IMD parts use a roll-to-roll heat transfer process such as those from Kurz or Nissha. A gravure-printed roll of film passes through the parting line of a specially designed mold, indexed and located using a specialized film feeder mounted to the platen of the molding machine. The carrier film with decoration is formed to the cavity geometry using vacuum. Only the decorative ink layers are transferred from the carrier film to the resin during the molding process, and the carrier film is no longer present on the part after molding. Common materials include polycarbonate (PC), acrylic, ABS, and PC/ABS.
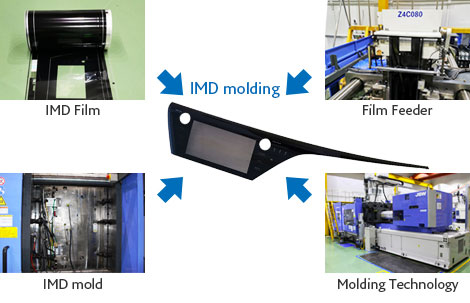
In-mold labelling (IML)
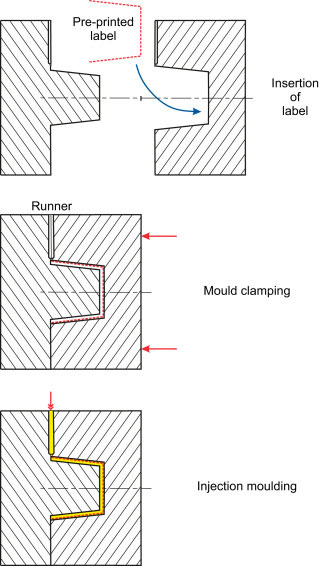
In-mold labelling is the use of paper or plastic labels during the manufacturing of parts by injection molding, blow molding, or thermoforming processes. The label serves as an integral part of the final product, which is then delivered as a pre-decorated item. This technique is used for the likes of dashboards, interior trims, and control panels.
The IML process requires special considerations for part and tooling design. Depending on the thickness of the chosen film—usually 180 to 380 µm—a minimum draft of 2° is required to ensure any hardcoat or first-surface printing won’t be damaged during ejection from the mold. Required applique coverage must be evaluated to keep the film from being caught at the parting line and to gauge potential edge light leaks. Excessive draw depth and resulting stretch during thermoforming can thin-out printed inks so they become translucent, and hardcoats can lose chemical resistance.
Many films are available for the durable IML process, with popular materials including polyester, polycarbonate, acrylic, and acrylic-capped PC. Formable hardcoats are used in many applications, which allow the decorated films to be thermoformed and then cured via UV exposure and placed into the mold. Typical cured coating pencil hardness ratings are 2H, which prevents most scratches on an automotive display lens.
Inks used in the IML process are specifically designed to survive exposure to the high temperatures seen during injection molding, and good bonding to films and molding resins. Tie-coats and primers can facilitate bonding between dissimilar materials. Color matching of the inks must be carefully checked using the full production material construction for the product; resin color can bleed through the inks and shift the observed color, so using finished molded parts for color evaluation is key.
IML often is used interchangeably with FIM.
Film-insert molding (FIM)
FIM involves inserting a thermoformed, die-cut screen or printed film into a mold and then injecting plastic around it. The film stays with the molded part.This method is used for decorative surfaces, functional components, and integrated sensors to improve the design, aesthetics, functionality, and durability of parts while streamlining the manufacturing process.
For successful FIM, factors to be considered include:
• Chemical resistance, environmental exposure—humidity, temperature cycling (inside the car it could be as harsh as -40 to +90 °C), heat aging and UV resistance; scratch resistance, finish requirements, and color and mechanical requirements such as flex modulus or impact strength.
• Proper design: typical molded-part design principles still apply, including consistent wall thickness, potential weld line locations, minimum draft, maximum rib-to-wall ratio to prevent sink marks, and minimum radii to reduce stress concentrations. Injection-molded parts and their tooling can be complex, as modifications to traditional molded part design and additional in-mold specific considerations are required.
• Birefringence (double refraction, as covered previously in DVN-I here and here), transmissivity and haze are reviewed when the decorated part is used as a cover lens for a display. Optical attributes mostly come from the molding resin, but the applique also will contribute to the optical qualities of the finished part.
• Resistance: film often is the first surface of the finished part, the part the user can touch. That means scratch and chemical resistance evaluation, along with various environmental exposure requirements, will determine whether the film passes or fails performance testing.
In-mold electronics (IME)
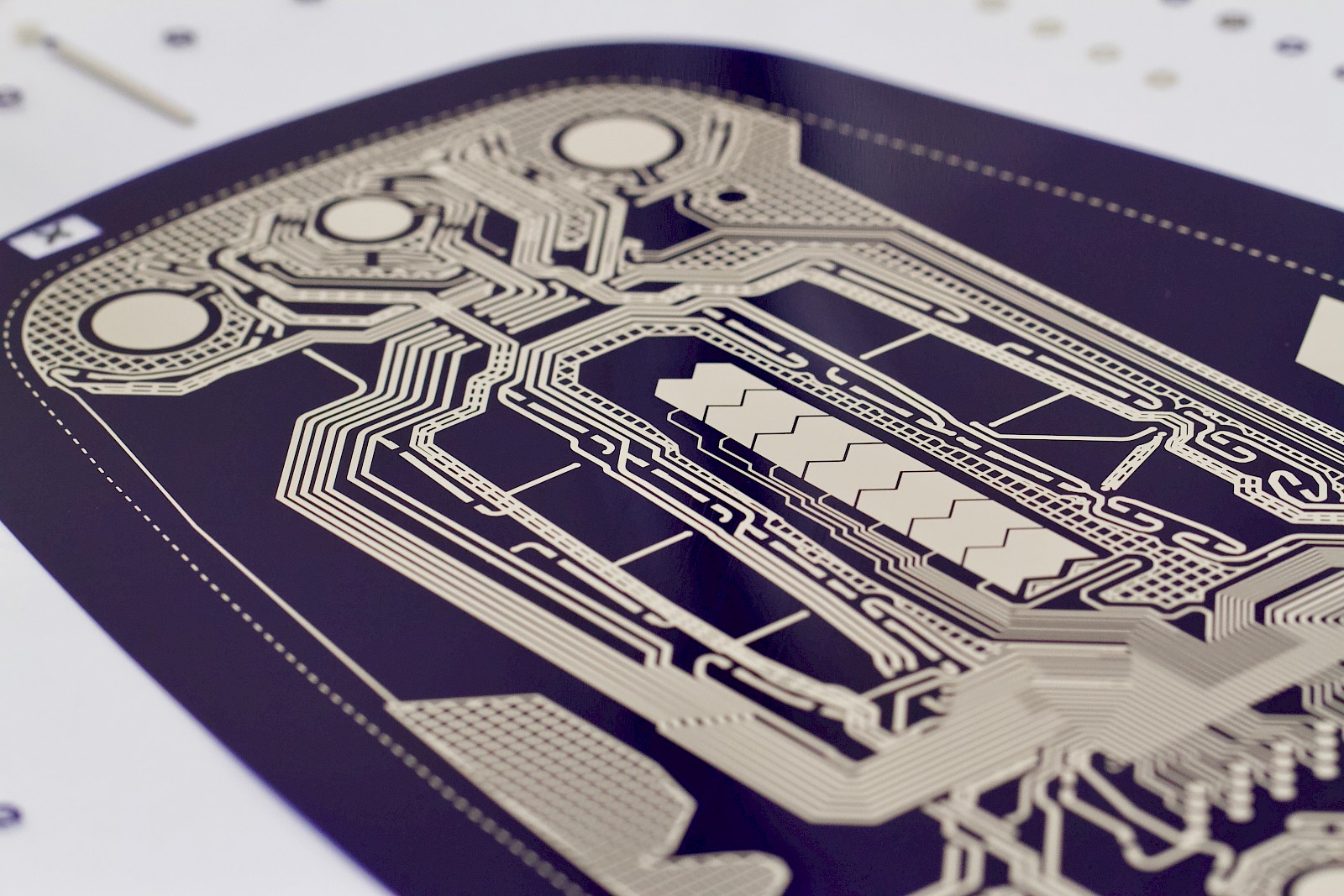
IME integrates electric and electronic parts like LEDs and conductive traces directly into the surface of molded plastic components. That adds functionality such as capacitive touch-switches or indicator lighting. The form factors and design envelope are not limited to planar parts; this technique is used for touch-sensitive control panels, lighting elements, human-machine interface elements (HMI), and remote controls. Specialist companies include Tactotek, Antolin, and Novares.
Antolin, WalterPack, and e2ip technologies, along with HMI partners, in 2023 established the IME Alliance, a global initiative focused on IME technology and manufacturing.
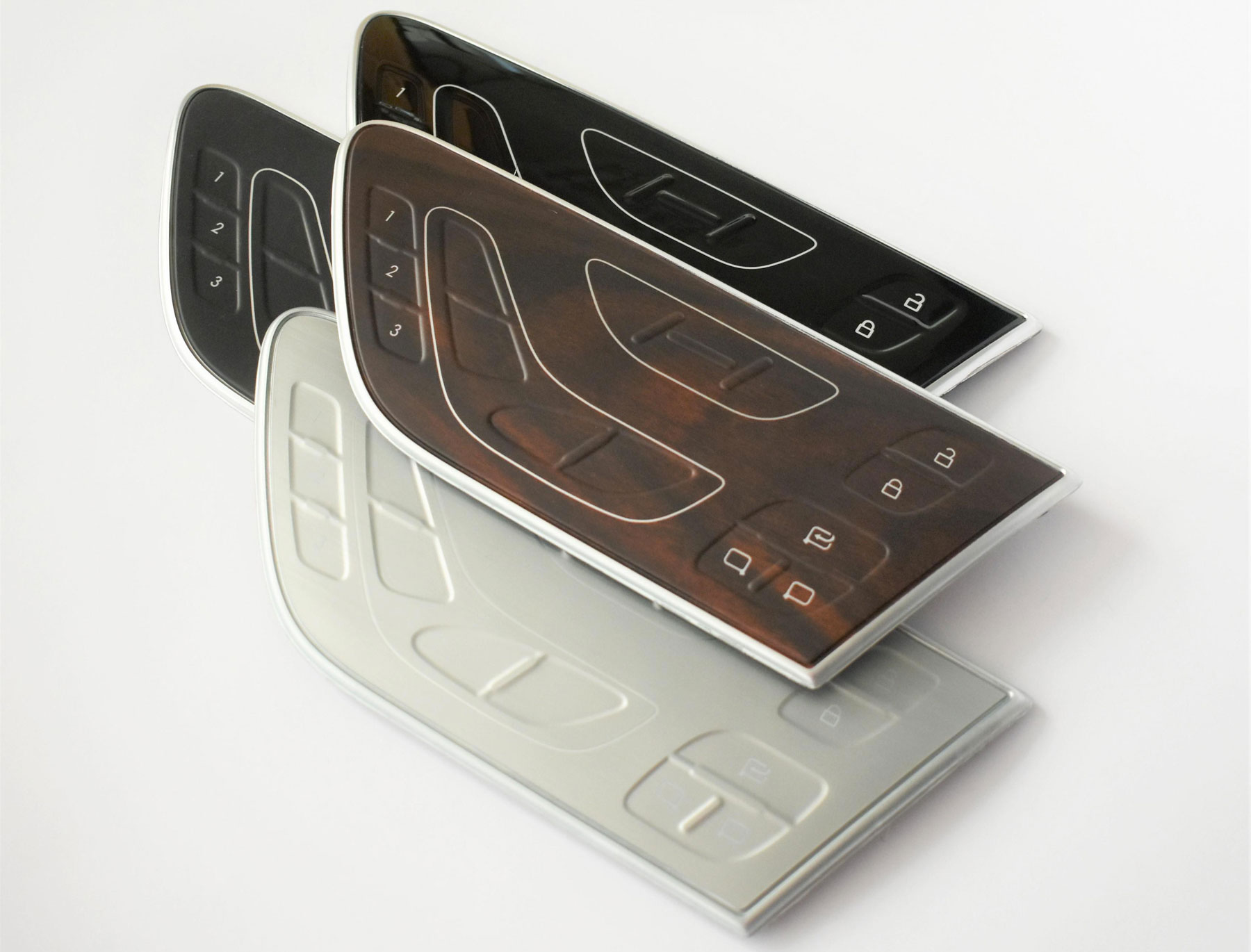
Interior Lighting
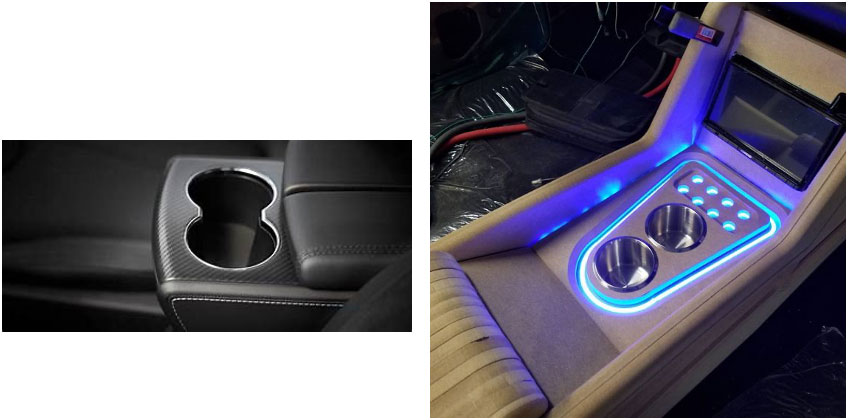
Static ambient lighting is a decoration element. Whether monochromatic or colorful lights, direct or indirect, premium and mainstream vehicles alike are equipped with static ambient lighting—”light is the new chrome”, so goes the philosophy, as described in detail many times in DVN-Interior Newsletters and Reports.
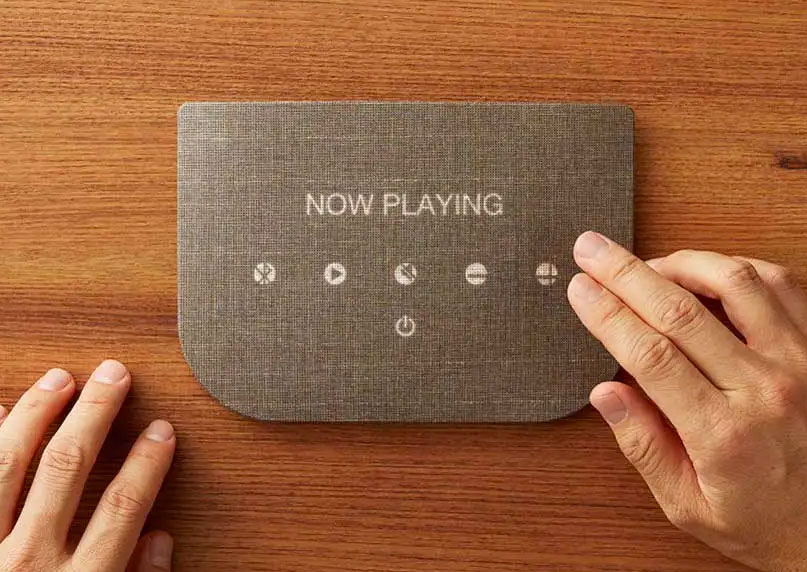
Sustainability
Combing plastic injected parts with film and/or electronics has to be evaluated for sustainability and potential end-of-life disassembly. It means the key ingredients of sustainable design and materials are crucial, as presented at last week’s Torino Workshop: eco-friendly materials, recycled plastics, natural fibers, plastic-free solutions, compatibility with circularity, reduced or even zero carbon footprint.
All in all
Materials, colors, and surface finishes for decoration are limited only by the creativity of the designers and manufacturing engineers, though high gloss continues to be popular for automotive applications. Textures can be screen-printed on the first surface, either full coverage or select areas. Texturing the mold will impart a texture to the final part, though the results often are visually different when compared to a part without an applique. If the applique is hard-coated, mold texture can fracture the hard coat and allow for chemical attack.
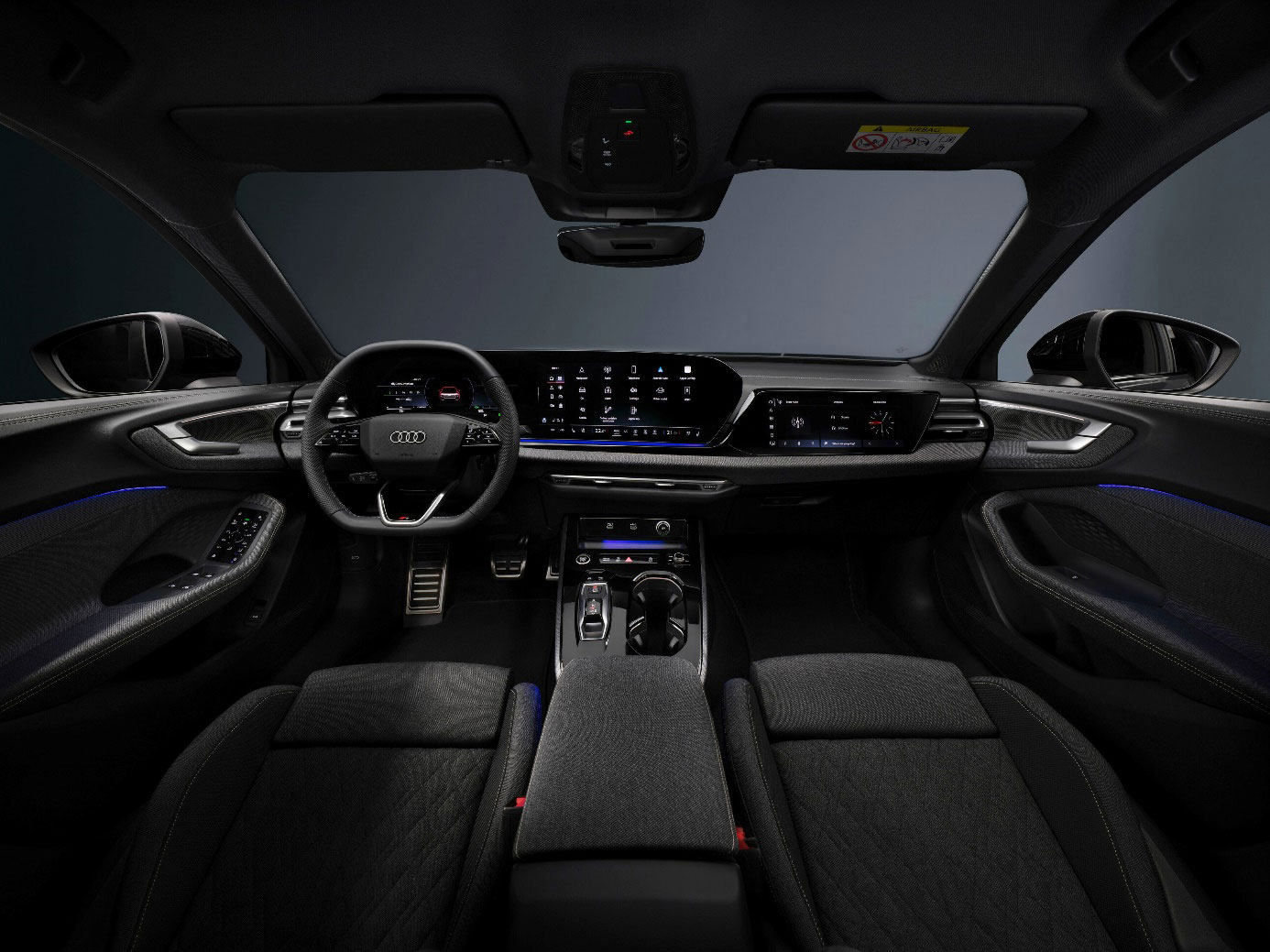
For an example of imaginative interior decoration, take the fascia of the instrument cluster and the center console of the new Audi A5. They bear several decorative inlays in aluminum trigon as well as two types of wood: walnut dark brown and fine grain ash natural.
In-mold decoration continues to progress with ever-more-complex designs and manufacturing processes. There are many options available to decorate almost any molded part this way. Material suppliers, printers, and molders cooperate to discover incremental improvements to push the limits of what can be achieved. There have been many failures along the in-mold product development road, of course, as with any other technology or technique. Nevertheless, the future has never been brighter for in-mold decoration manufacturers and their supply chains.
References in DVN Interior